The optoelectronic pod of unmanned aerial vehicle system is a navigation control technology application product based on inertial navigation technology, which can effectively isolate the angular motion interference caused by carrier movement on optoelectronic sensors, and achieve the recognition, tracking, and locking functions of task targets. Its most essential function is to achieve long-distance reconnaissance and high-quality imaging. The selection of different pod parameters and the highest functional requirements are the operating distance, which is the most core requirement of the pod. All structural design, equipment combination, weight control, performance index balance, etc. are based on the requirements of the operating distance.
At present, small and medium-sized unmanned aerial vehicle systems have a concentrated weight range of 1 kg to 5 kg for mounted pods. There are several common functional requirements for pods: target search, target recognition, target tracking, and target positioning. According to different imaging principles, it can be divided into two types: visible light imaging and infrared thermal imaging. The tracking and positioning function can be calculated by the relative position between the target and the drone or pod, or achieved by adding a laser rangefinder to the pod.
Analysis of the main technical parameters of commonly used optoelectronic pods for small and medium-sized unmanned aerial vehicles.
Due to the numerous parameters involved in the pod, for ease of description, we will now analyze a typical product from UnionTech.
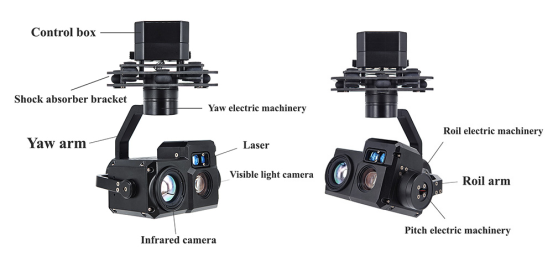
Generally, manufacturers provide basic information such as the structure, weight, and dimensions of the pod, with the most crucial indicator being stability and accuracy.
Due to the special working environment, the suspended cabin needs to continuously and effectively isolate the motion interference caused by the motion of the unmanned aerial vehicle platform on the photoelectric sensor. It will be affected by various factors such as the vibration, attitude changes, and wind resistance moment of the unmanned aerial vehicle. In order to ensure stable and clear imaging of the imaging equipment, the suspended cabin must ensure the continuous stability of the visual axis in the inertial space, that is, the improvement of stability accuracy (stability accuracy is generally measured in radians, where the definition of radians is to convert the center angle of a circle corresponding to 1/360 of the circumference into a 1 degree angle, denoted as 1 °, 1 °=60 minutes, and 1 minute=60 seconds. In addition, the center angle of a circle corresponding to a radius equal to a long arc is called a 1 degree angle, denoted as 1 (rad). 1 rad is approximately equal to 57.3 °. Stability accuracy, maximum angular velocity, and maximum angular acceleration can be understood as the stable level and response speed of the pod operation.
Tracking accuracy is another core indicator of the pod, which is the ability to track fixed or moving targets under certain disturbance conditions and keep them in the center of the field of view, directly related to indicators such as illumination accuracy and target positioning accuracy. But tracking accuracy is a comprehensive indicator, which is not only related to the control accuracy of the servo system, but also to the tracking effect, lighting intensity, and visibility of the image tracker. This indicator is based on strong capabilities and is generally rarely mentioned in the civilian field.
In addition, the concept of "frame" and "axis" will be involved in the structure of the pod. Small and medium-sized unmanned aerial vehicles often use two or three axis pods. Due to the general requirements of compact and lightweight pods, as well as good environmental adaptability, the most commonly used structure is "two axes and two frames". The three axis pods add a roll axis outside the orientation and pitch axis of the two axis pods. Which is better, two axis or three axis? The three axes increase the roll direction, and it also plays a role in avoiding target loss when the drone turns or exceeds the target at an excessive angle. But there is one more structure and one more hidden problem, and the weight of multiple structures needs to be comprehensively considered.
In addition, every student majoring in aircraft design is dedicated to reducing the weight of the aircraft, so the pod subsystem also has typical characteristics of system integration. The components of each pod manufacturer are purchased from shelf products, and the level of integration ability is most directly reflected in the system weight. So, when comparing pod products, it can be found that many indicators are similar or even the same, but the weight and size are absolutely different, which to some extent reflects the different design concepts and integration capabilities of each company. However, the loading pods of small and medium-sized drones are generally of lower mass, and manufacturers can refer to their "big ball" design and integration capabilities when selecting them.
Visible light imaging
Visible light imaging relies on the physical imaging performance of reflected light, which is limited by the number and intensity of reflected light. It mainly focuses on main indicators such as image elements/resolution, focal length, field of view, and zoom ratio.
Element/Resolution: Pixels refer to small squares of an image that have a clear position and assigned color values. The color and position of these squares determine the appearance of the image. Pixels can be regarded as indivisible units or elements in the entire image. Usually, "resolution" is expressed as the number of pixels in each direction, such as 640X480. Resolution is directly related to the pixels of an image. A resolution of 640 x 480 in an image can reach 307200 pixels, commonly known as 300000 pixels.
Focal length refers to the distance between the main point of an optical system's image and the main focus. Assuming that the same subject is photographed at the same distance, the longer the focal length of the lens, the greater the magnification of the image formed by the subject on the film or image sensor.
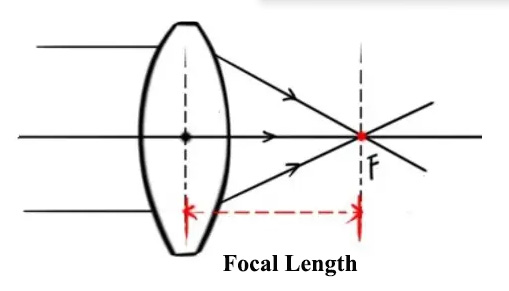
The field of view represents the maximum range that can be observed, usually expressed in terms of angle. The size of the field of view angle determines the field of view of the optical instrument. The larger the field of view angle, the greater the field of view. Simply put, if the target object exceeds this angle, it will not be captured in the lens. The relationship between field of view and focal length: In general, the larger the field of view, the shorter the focal length.
Zoom Ratio, also known as optical zoom, refers to the ratio of the shortest and longest focal points of a zoom lens. The larger the zoom ratio, the greater the change in the viewing range. However, it is a ratio that cannot fully reflect the zoom level and performance of the camera lens. It should be noted that digital zoom/digital zoom is achieved by enlarging a fixed photo through software means and compensating it through certain algorithms, so digital zoom has no practical significance. Because optical zoom is achieved through physical means, that is, by adjusting the distance between the lenses of the hardware, it only changes the distance of light transmission, and the light itself does not change, so the imaging quality will not change.
Infrared thermal imaging
Infrared thermal imaging is because all objects in nature with temperatures higher than absolute zero (-273.15 ℃) are constantly radiating infrared radiation. Different objects have different radiation temperatures, and the radiation intensity varies. Therefore, the infrared radiation characteristics formed by the temperature difference or radiation difference between the target and the environment or between different parts of the target can be used to form images, and ultimately used to discover and identify targets.
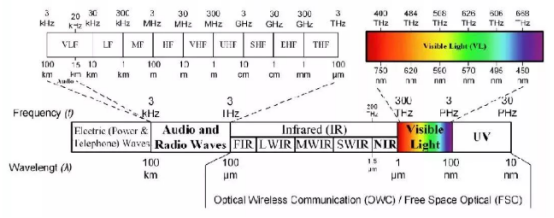
The actual infrared band that can be detected and utilized by humans only accounts for a small part of the entire infrared radiation band. The infrared thermal imaging of the pod mainly focuses on main indicators such as pixel size, resolution/number of pixels, noise equivalent temperature, and minimum distinguishable temperature difference.
Pixel size: In infrared imaging systems, small pixels mean an improvement in object resolution; The infrared detection system, with large pixels, means stronger energy harvesting capabilities.
Resolution/Pixel Number: It is an important parameter for measuring the quality of a thermal imager detector, representing the number of unit detection elements on the detector's focal plane. The higher the resolution, the clearer the imaging effect.
NETD: Noise equivalent temperature is a measure that characterizes the temperature resolution of an infrared imaging system limited by objective signal-to-noise ratio. It is also known as thermal sensitivity, which is the minimum temperature that a thermal imager can distinguish. A smaller NETD indicates better image quality.
MRTD: The minimum distinguishable temperature difference, which comprehensively describes the spatial and temperature resolution ability of infrared imaging systems to targets when imaging in noise.
The infrared detectors used in the pod can be divided into two categories: refrigerated and non refrigerated. Refrigerated infrared detectors have many advantages, such as faster response speed, finer image details, higher sensitivity, longer detection distance, and more stable performance. However, performance advantages need to be demonstrated in low-temperature environments. This makes the cost of refrigeration type infrared detectors high, with a large volume and weight, mainly used in military and scientific research fields. The imaging detector of non cooled infrared thermal imagers does not require low-temperature cooling. Scene changes can cause temperature changes in the infrared detector, which are converted into electrical signals and processed to generate images. The equipment is compact, low-cost, and has a long service life, but its accuracy is relatively poor. It is widely used in areas where imaging performance is not high. Non cooled infrared detectors are mainly used for hanging pods on small and medium-sized drones.
Other parameters
Laser rangefinder refers to an electromagnetic wave rangefinder that uses a laser as a light source, and its indicators mainly focus on ranging range and ranging accuracy. In addition, according to different project requirements, attention should also be paid to the environmental temperature and working temperature that the pods meet, as well as the types of mechanical and electrical interfaces, especially communication interfaces, video output interfaces, and communication protocols. There are many communication interfaces that can be selected in industrial sites, and the common ones are as follows: serial port 232, 422, 485, Ethernet port, GPIB, USB, wireless, fiber optic, etc. Among them, the commonly used communication interfaces for pods are 232, 422 or Ethernet port. There are many video interfaces as follows, among which the commonly used video interfaces for pods are HD-SDI, HDMI, Ethernet ports, etc.
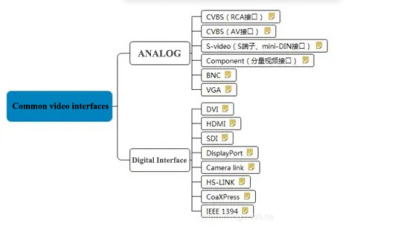
Other considerations in the selection of optoelectronic pods for small and medium-sized unmanned aerial vehicles
The application scenarios of small and medium-sized drones are diverse, and different task payloads need to be mounted according to the task scenario. Requirements for fast loading and unloading structures are proposed for the pods, and as the cruising speed requirements increase, pods manufacturers can plan for embedded structural design. In some specific operating environments, it is also necessary to consider the dust-proof, anti fog, and anti-corrosion capabilities of the pod. Of course, in the process of selecting pods, it is necessary to comprehensively consider factors such as product compatibility, reliability, and project cost, as well as the supply cycle and after-sales service capabilities of the pods manufacturer. More importantly, actual testing is conducted to verify the effectiveness of the manufacturer's provided pod parameters, check the quality of the received video images, and then determine the most suitable pod after meeting project requirements.